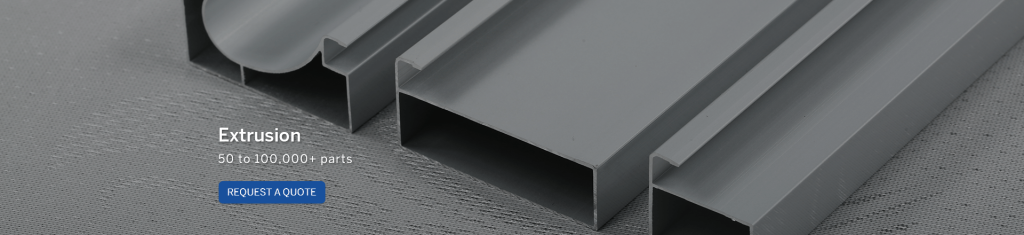
Aluminum extrusion is a technique used to transform aluminum alloy into objects with a definitive cross-sectional profile for a wide range of uses. The extrusion process makes the most of aluminum’s unique combination of physical characteristics. Its malleability allows it to be easily machined and cast, and yet aluminum is one third the density and stiffness of steel so the resulting products offer strength and stability, particularly when alloyed with other metals.
The Process of Aluminum Extrusion
The process of aluminum extrusion consists of the following steps:
∙ After designing and creating the shape of the die, a cylindrical billet of aluminum alloy is heated to 800°F-925°F.
∙ The aluminum billet is then transferred to a loader, where a lubricant is added to prevent it from sticking to the extrusion machine, the ram or the handle.
∙ Substantial pressure is applied to a dummy block using a ram, which pushes the aluminum billet into the container, forcing it through the die.
∙ To avoid the formation of oxides, nitrogen in liquid or gaseous form is introduced and allowed to flow through the sections of the die. This creates an inert atmosphere and increases the life of the die.
∙ The extruded part passes onto a run-out table as an elongated piece that is now the same shape as the die opening. It is then pulled to the cooling table where fans cool the newly created aluminum extrusion.
∙ When the cooling is completed, the extruded aluminum is moved to a stretcher, for straightening and work hardening.
∙ The hardened extrusions are brought to the saw table and cut according to the required lengths.
∙ The final step is to treat the extrusions with heat in age ovens, which hardens the aluminum by speeding the aging process.
Additional complexities may be applied during this process to further customize the extruded parts. For example, to create hollow sections, pins or piercing mandrels are placed inside the die. After the extrusion process, a variety of options are available to adjust the colour, texture and brightness of the aluminum’s finish. This may include aluminum anodizing or painting.
Today, aluminum extrusion is used for a wide range of purposes, including components of the International Space Station. These diverse applications are possible due to the advantageous attributes of aluminum, from its particular blend of strength and ductility to its conductivity, its non-magnetic property and its ability to be recycled repeatedly without loss of integrity. All of these capabilities make aluminum extrusion a viable and adaptable solution for an growing number of manufacturing needs.
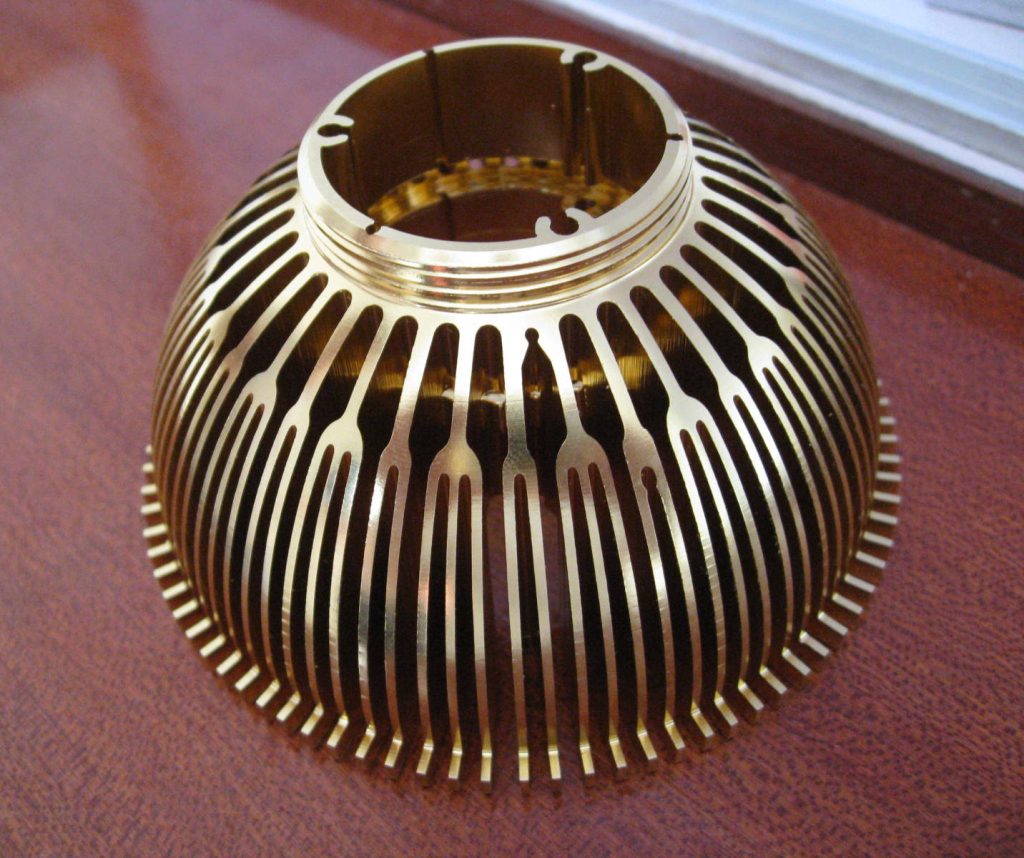
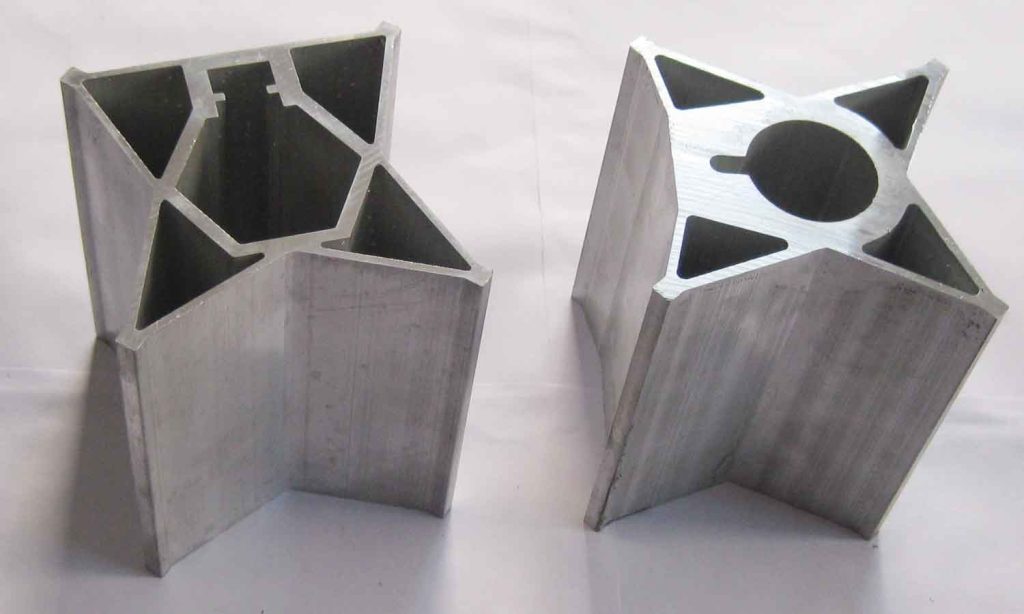