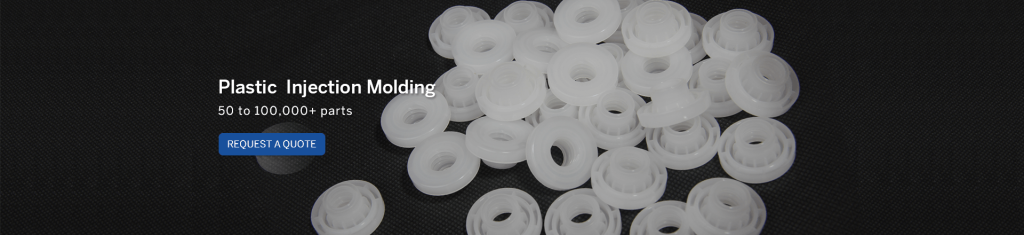
Plastic Injection Molding
At Mockup Technology, we specialize in high quality plastic injection molding and mold tool making. Plastic injection molding is by far the industry’s most common way to manufacture parts, especially when making larger quantities. We provide plastic injection molding for 50 to 100,000+ parts as well as a wide range of other manufacturing and finishing services to complete your project.
What is Plastic Injection Molding?
Plastic injection molding involves melting granular plastic pellets into a liquid form and then compressing this liquid into the empty cavity of a mold tool.
The plastic will retain the shape of the mold as well as the surface texture of the walls of the cavity.
After an optimized injection and cooling phase, the now solidified plastic part is ejected and the molding cycle is repeated.
This molding cycle can take from as little as a few seconds to several minutes depending upon part size, molding resin and part design.
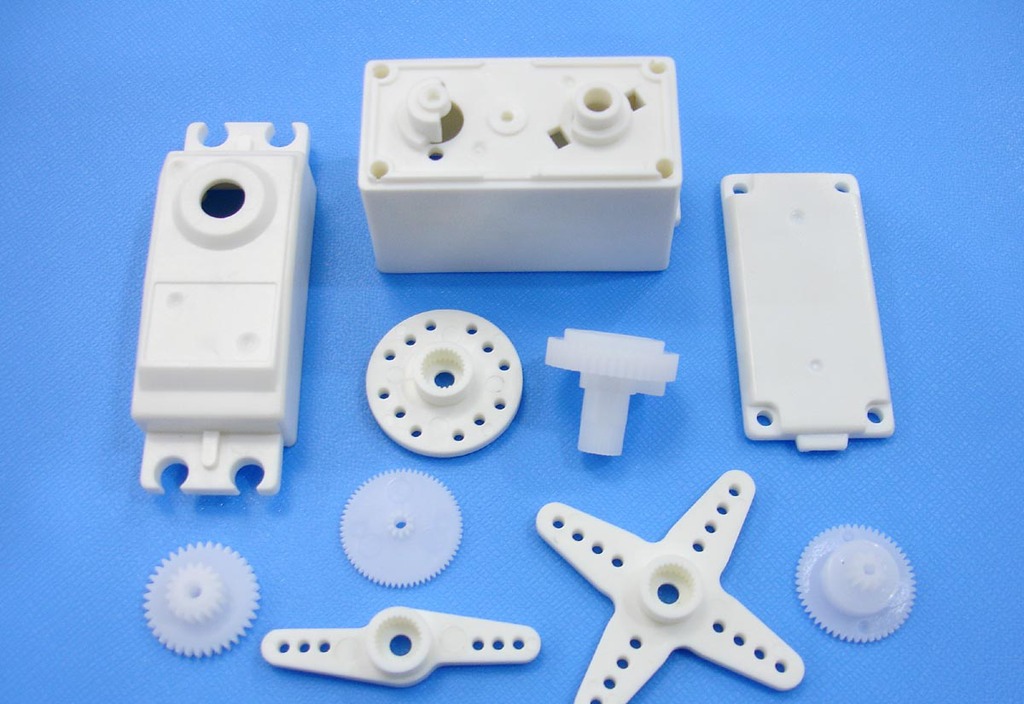
Advantages of Plastic Injection Molding
∙ We have thousands of different types of plastic are available for you to choose from, for a wide range of mechanical and cosmetic properties.
∙ Plastic injection molding makes more economic sense for larger volumes. For smaller volumes we might recommend other services like CNC machining, vacuum casting or 3D printing depending on the needs of your project.
∙ Hundreds of thousands of moldings can be produced from a single mold.
∙ Your part can have excellent surface quality finishes in a wide range of polishes and textures.
∙ Over-molding is available to combine different types of plastic in one piece.
∙ It is ideal for lightweight parts that are immune to corrosion.
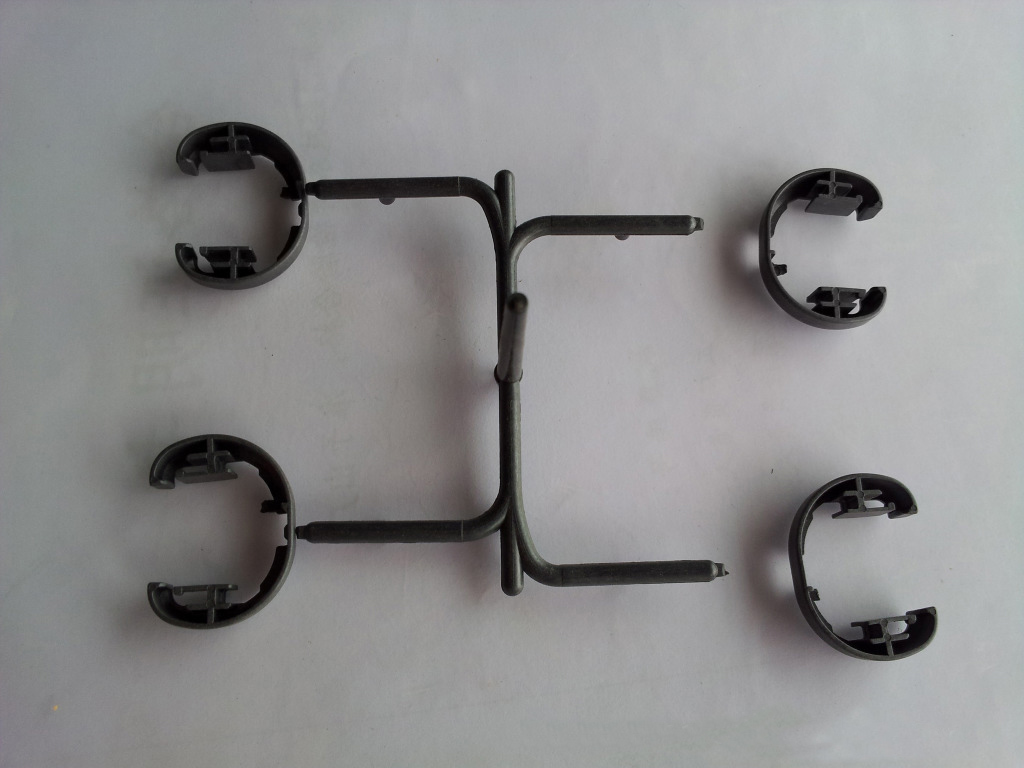
Mold Tool Production
Materials such as aluminum 7075, pre-hardened tool steel such as P20 and fully hardened tool steels like H13 are most commonly used when making your mold tool.
The material used will depend on the number of parts you wish to produce.
Aluminum Tooling
Aluminum tools are quickest to produce and most cost effective. Aluminum is softer and therefore suited to smaller volumes. For larger volume production, and for aggressive resins or part geometries requiring thin blades or ribs it’s best to use harder materials that are more durable.
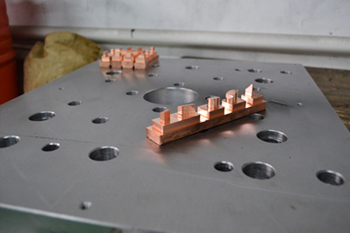
Steel Tooling
Steel tools are tougher and more durable but can take longer to produce. These are suited for larger
volumes or when injecting abrasive or corrosive plastics that would damage aluminum molds.
∙ Pre-hardened tool steel is used for quantities of 100K pcs and more, depending on plastic material and part geometry. We use P20 and NAK80 stress-relieved steel.
∙ Fully-hardened tool steel is the most durable and can be used for millions of injected parts.
H13 hardened steel is ideal for full production volumes or when injecting abrasive engineering
-grade plastics.
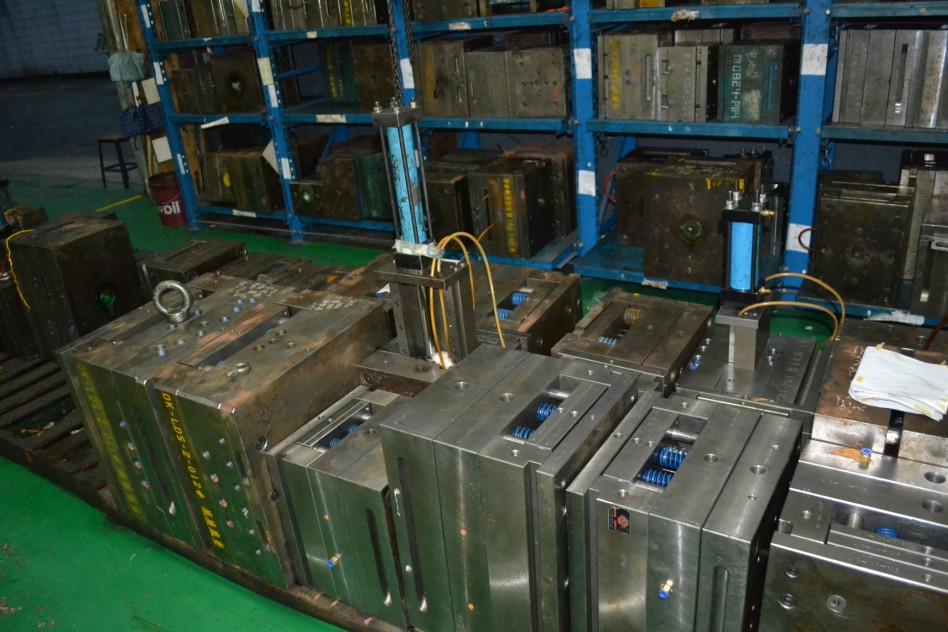
Part Production
When producing parts, a variety of polymers are available including thermoforming plastics, thermosets and some elastomers. Mold tools and the injection process are both carefully engineered to match the unique requirements of each material in order to produce the highest quality finished parts. Thermoforming plastics are relatively softer, more flexible, less durable, and easily recycled whereas thermosetting plastics are more rigid, durable and expensive and cannot be repaired or recycled once formed. Find out more about materials you can choose from by looking out our materials sheet and tolerance guide.